

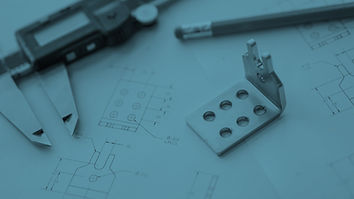
PROCESS
WHAT TO EXPECT WHEN YOU
PARTNER WITH METALFAB GROUP
MetalFab Group has worked with a wide variety of clients on an even wider range of projects. Whether you’re an engineer, a buyer, or totally uninitiated to the industry, we make sure to collaborate with you throughout the entire process to ensure that you are comfortable every step of the way.
A QUICK LOOK AT OUR PROCESS
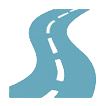
STEP ONE
EXPLORATION
MetalFab Group has worked with a wide variety of clients on an even wider range of projects. Whether you’re an engineer, a buyer, or totally uninitiated to the industry, we make sure to collaborate with you throughout the entire process to ensure that you are comfortable every step of the way.


STEP TWO
QUOTING
After we have an overall idea of the scope of the project, we can begin on the quoting phase. To create a quote we need a dimensional print, which could be something as simple as a sketch on a napkin with dimensions indicated, to a full scale CAD file. We also consider the material (type and thickness) from which the part will be made, as well as the desired quantities of the part. And we will also ensure that we have your contact information (and that you have ours!) so that you can ask us any questions, and we can contact you as soon as we have the quote ready.
Once we have the required specifications we will get you a quote back within 24 hours. We’ll restate the details and give you a price breakdown. Depending on the project type, we might also give options and/or deviations to either reduce cost or improve quality.
At this point it is up to you to either approve and accept the quote, or to call for a re-quote that might call out specific changes, updates or variations.
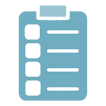
STEP THREE
ORDERING
Upon approval of the quote, we then move the project to an official order status. Each order is accompanied by a print to which each phase of production will use to measure tolerances and accuracy. In the case that you did not supply a solid model or DXF file for your quote, we can create one for your approval.
Accepted File Types:
> Solid models (CAD files)
> DXF (Flat Parts Only)

STEP FOUR
PRODUCTION
Once your order has been created, we can then move your project into production where we will begin fabrication. Our experienced manufacturing team and our quality control personnel take over from here, working with you to ensure that the finished product meets or exceeds your expectations.

SERVICES | THE OTHER GUYS | THE METALFAB EXPERIENCE |
---|---|---|
Laser Cutting | ✔ | ✔ Up to 1" thick steel |
Folding Capabilities | ✔ | ✔ Up to 120" wide |
Finishing | ✔ | ✔ Deburring, Grinding, Powdercoating and Polishing |
Welding | ✔ | ✔ Skilled TIG, MIG, Spot and Robotic Welding |
CNC Milling | x | ✔ RPM: 12,000; Travel Dims.: X: 30", Y: 16", Z: 20" |
ISO Certified | x | ✔ ISO 9001:2015 |
Tube Bending | x | ✔ 1-1/2" to 3-1/2" Tubing Mandrel Benders |
NSF Standards | x | ✔ Food Industry Safe Manufacturing |
Design Services | x | ✔ In-House Engineering Team |
-
What do I need to get a quote?We need a few things for an accurate project quote. A print is the best case scenario, but barring that we can also quote from a sketch with dimensions, material, thickness, and quantity.
-
Which industries do you work in?We primarily make products for the Aerospace, Automotive, Food Service, and Construction industries. In these fields our staff has a wide array of knowledge needed to assist in navigating any regulatory issues that may arise during production. Our team is trained in specific techniques to be sure the product we build works seamlessly in the industry of its designation. As an example: for projects within the Food Service industry, we design and manufacture your design to minimize or eliminate bacteria traps and keep food safe.
-
I need something made for food service. Do you have experience in that?We’ve built products for many food service manufacturers and have lots of experience with regulations and best practices. Some common pitfalls a company will make is not eliminating bacteria traps in design, not using passivation in welds, and not using the correct materials. You don’t have to worry about that with us. We have a ton of experience adhering to NSF Standards and can guide you through the development of a product that not only works for your customers but is also safe to use.
-
I don't have a drawing, can you help?Yes! We only need a sketch and a conversation to get started working together. Our engineering and sales team will guide you through the process step by step and will strive to make suggestions for the best outcome based on our experience.
-
I only have a few parts to make, do you accept really small runs?Sure. We are capable of small yield runs, but pricing gets better as the quantities go up. Our sweet spot for small jobs is 25 pieces, but this can be highly dependent on complexity, material, etc. If you’re looking for big quantities, we’ve completed projects as high as 15k pieces!
-
I need five-thousand parts made in one week. Can you do it?It depends on complexity and the amount of processes involved. Short answer: Yeah, we can handle a rush job like that. Our average turnaround is two weeks but this can fluctuate wildly. A strictly laser-cut product can be ready in days, while a complex enclosure can take up to 4 weeks.
-
I need a one-off muffler made for my _____. Can you guys help?We primarily work for other businesses though we are experts in muffler and exhaust system design. If you are looking for a one-off muffler for a personal project, it will most likely be cost prohibitive. Although we once built an exhaust system one-of-a-kind for a P51 Mustang! That was a sweet project.